Equipment Operational/Non-Operational-HQ
Equipment downtime can be monitored in HQ and managed by both back-office staff and technicians by setting the equipment status to operational or non-operational. Monitoring and quick restoration of equipment operation enhances reliability, leading to improved customer satisfaction. For service-oriented businesses, maintaining operational equipment is crucial for meeting service level agreements (SLAs) and ensuring timely delivery of services. When a piece of equipment becomes non-operational, an HQ user or a technician can designate a piece of equipment as non-operational. This provides visibility to both Back-Office personnel and Technicians. This can be done within HQ or the Service app. Click here to learn more on how a Technician can change the operational status of Equipment within the Service app. NOTE: This feature does not integrate with your business system. By default, all equipment is set to Operational until changed to Non-Operational.
To change a piece of Equipment to Non-Operational in HQ
This can be changed via Admin>Equipment>Equipment Details screen or via Service>Dispatch>Work Order Details screen (if the equipment is assigned to a work order).
To change a piece of equipment from Operational to Non-Operational in the Equipment Details screen:
- Navigate HQ>Admin>Equipment. Search for the piece of equipment you'd like to change the operational status of and click the 3 dots to the right of the equipment and select Details. TIP: Enable the Filter option: Equipment Operational and enable the Column option: Equipment Operational. Selecting Yes or No within the Equipment Operational filter will help narrow down the list of equipment.
- Locate the Equipment Operational Card within the Equipment Details Screen. Within the card, select the red x icon to mark equipment as non-operational. TIP: There are several column options you can choose from to display a variety of information relating to this card. Enable any you'd like to have by clicking on the Column icon within the card and selecting the column options you want.
- Next, confirm or select your date/time the equipment became non-operational and select Save. NOTE: By default the current date/time will pre-populate.
To change a piece of equipment from Operational to Non-Operational in the Dispatch>Work Order details screen:
- Navigate HQ>Service>Dispatch screen/table view. Locate the work order the equipment is assigned to and select it. TIP: Enable the Filter option: Equipment Operational and enable the Column option: Equipment Operational. Selecting Yes or No within the Equipment Operational filter will help narrow down the list of equipment. NOTE: These filter and column options are ONLY available in Table View.
- Within the work order details screen of a work order, under the Equipment card, click the edit icon to change the equipment from Operational to Non-Operational and vice versa.
- Next, confirm or select your date/time the equipment became non-operational and select Save. NOTE: By default the current date/time will pre-populate.
Once designated in HQ, a Technician can see this within the Service app Work Order Details screen. If the equipment is Operational, within the Equipment card, the Edit icon will be WHITE. If the Equipment is Non-Operational, the edit icon will be RED.
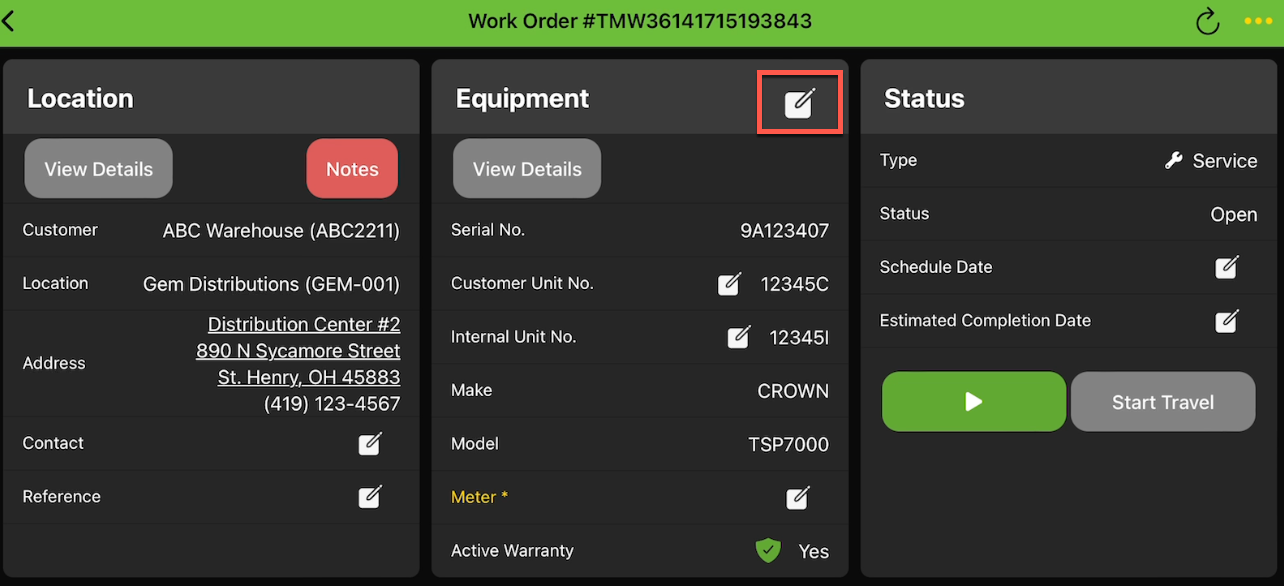
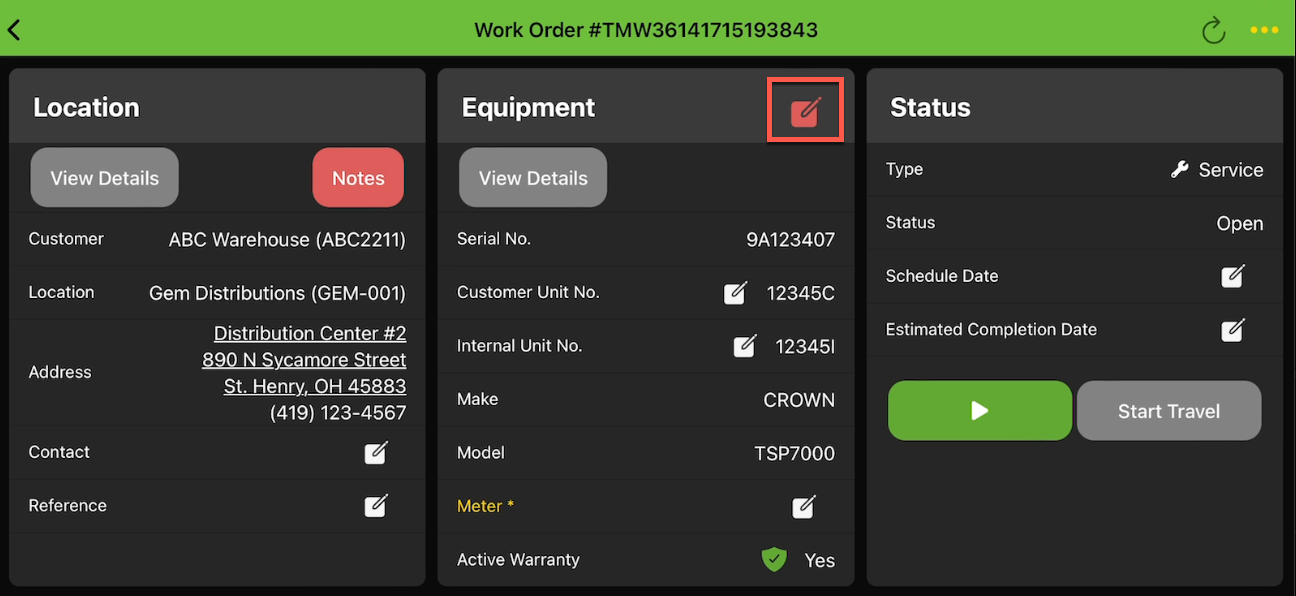
Click here to learn how to mark equipment operational or not operational in Tinnacity's Service app.